Artistic casting is a discipline that combines art, science and tradition. Throughout the history of casting, this technique has allowed the creation of metal sculptures, with materials such as bronze, stainless steel or brass. The strength and mechanical properties of these metals have allowed them to become the basis for numerous works of art. Among the casting methods, the lost wax technique is one of the oldest and most refined, and has been used since ancient times to the present day.
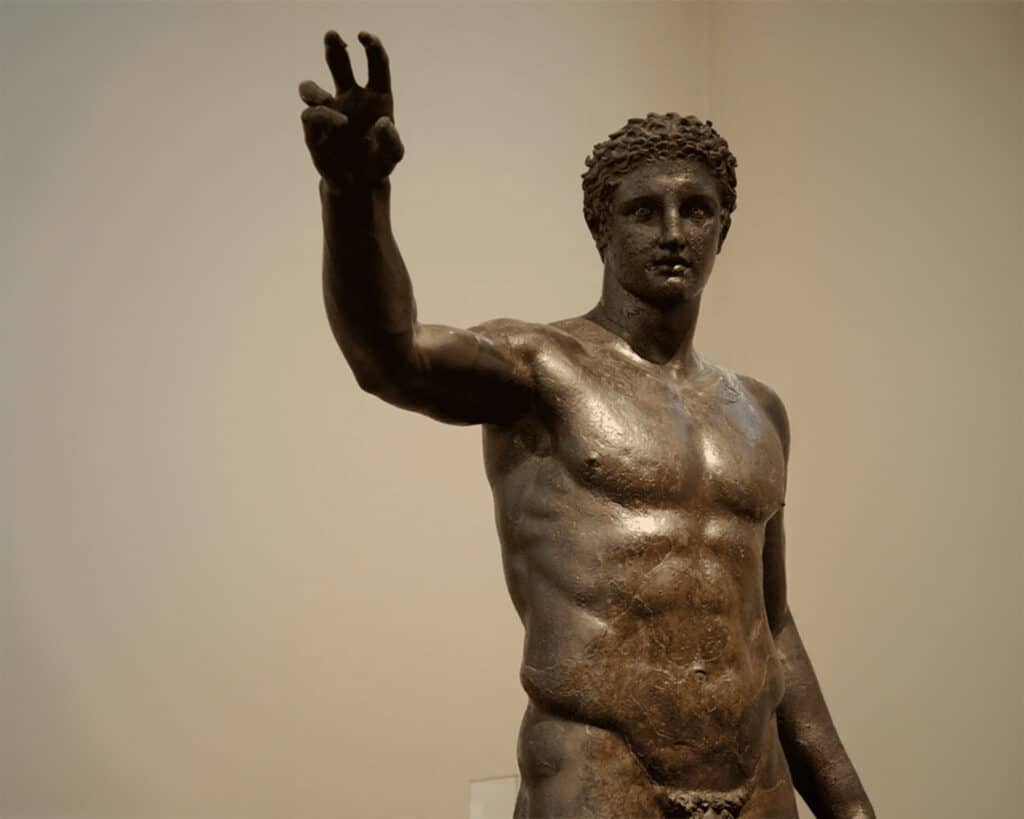
The Evolution of the Foundry in Art
From ancient Egypt or Greece, to the Renaissance and contemporary art, metal casting has been a fundamental process in the creation of sculptures. In its beginnings, techniques such as sand casting and foundry molding were used, processes that have evolved over time. Today, the production of sculptures combines tradition in casting with technological innovation, allowing the manufacture of pieces in less time, at lower costs and with a range of finishes and more complex shapes.
The foundry workshops have been spaces where the creativity of the artists and the technical knowledge of the foundrymen converge.In these spaces, foundry masters have developed a manufacturing process not only focused on producing high quality pieces, but also on optimizing resources and reducing environmental impact through the use of refractory materials and efficient processes.
The Lost Wax Foundry
The lost wax technique is one of the most widely used techniques for sculpture over the centuries, allowing all the details to be recorded with high fidelity to the original model. Its process consists of different stages:
- Modeling. The artist creates a model of the sculpture in a resistant material that allows a mold to be made on it. Clay, hardened plasticine, coated polystyrene or models obtained by 3D printing, an increasingly common technique that allows complex shapes to be made with great accuracy, as explained in this Museo del Prado guide to sculptural techniques.
- Silicone mold. From the model, a silicone mold is made, capable of capturing even the smallest detail. From this mold, a wax reproduction is obtained, which is carefully reviewed and prepared for the following stages of the process.
- Ceramic bath. The wax figure is then coated with layers of refractory material, forming a ceramic shell that will faithfully record its shape. This coating must therefore be resistant to high temperatures to allow the metal to be cast.
- Casting and pouring. By means of heat, the wax is removed from the inside of the shell, leaving an exact gap to be filled with the molten metal.Bronze, brass, white bronze, aluminum or stainless steel can be used at this stage, depending on the desired finish and properties of the final piece.
- Cooling and demolding. Once the metal has cooled, the ceramic shell is broken and the sprues or channels that facilitated casting are removed. The resulting metal piece is ready for further finishing and patina work.
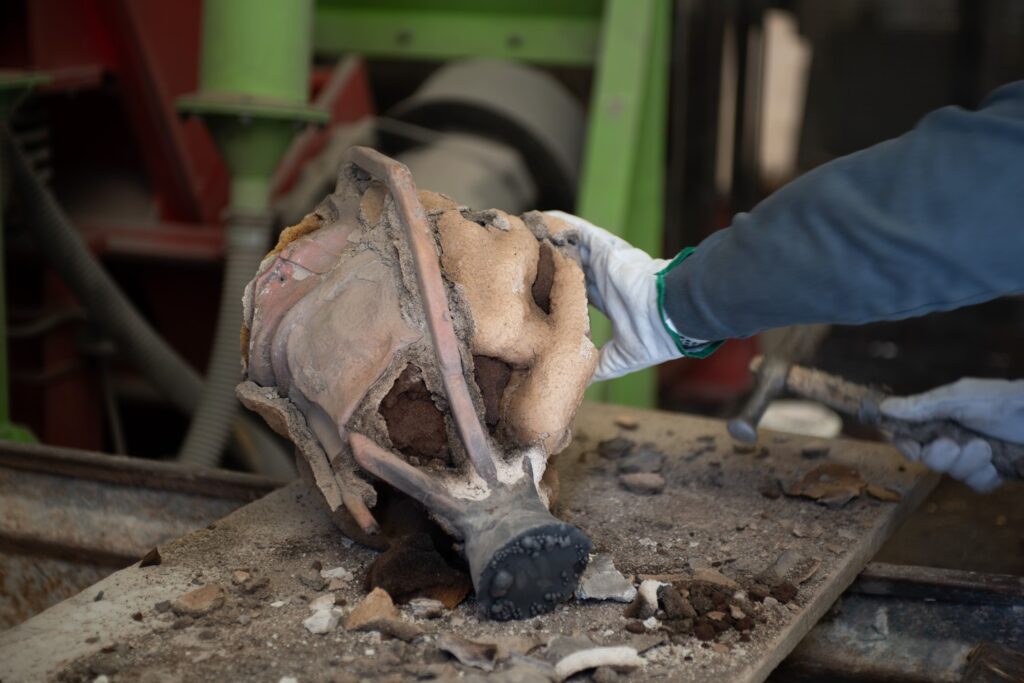
This creative process, which has been perfected over the centuries, remains the preferred choice of many sculptors due to its precision and ability to reproduce complex shapes with high quality.
Materials in Sculptural Foundry
Depending on the artist’s intention and the environment in which the work will be exhibited, different metals can be used in the artistic casting:
- Cast bronze. Classic and versatile, it is the material of choice for bronze sculpture due to its strong resistance and ease of capturing detail. Its composition usually includes both copper and tin.
- Stainless steel. Provides a contemporary aesthetic with reflective finishes and high resistance to corrosion, ideal for monumental sculpture in outdoor spaces.
- Brass. Its golden hue makes it a striking option, especially in pieces that seek to stand out for their color and texture.
- Iron casting. It is used in heavier and ornamental structures due to its solidity.
The choice of material influences the casting techniques and the subsequent treatment required for the sculpture, from the type of patina to the final assembly technique.
The importance of Innovation in the Foundry
Over the years, the foundry has incorporated technology to optimize the process without losing its artisanal essence. Today, foundries use digital tools to improve efficiency in the production of sculptures and reduce environmental impact, promoting sustainability in the foundry.
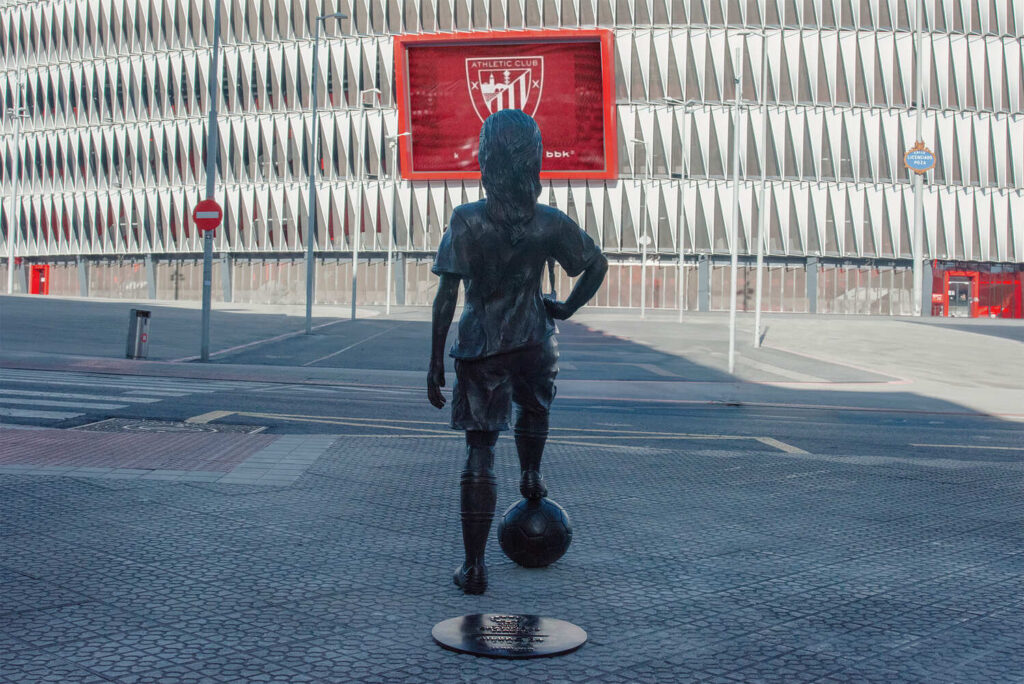
Sculptural techniques have evolved to adapt to large-format sculptures and optimize the use of materials in the creation process. They also seek to guarantee the durability of each piece, respecting the quality and integrity of the original design.
The use of high-temperature furnaces makes it possible to work with demanding metals and achieve precise melting. Quality control systems ensure that each job achieves the optimum finish and strength.
The Foundry as a bridge between Art and Eternity
Cast sculptures have stood the test of time, retaining their beauty and expressiveness over the centuries. This process combines technical know-how and artistic sensitivity, and is still essential in contemporary sculpture. It also allows creators to transform their ideas into immortal works that endure over time.
From its origins to the present day, artistic casting has evolved, but still maintains its essence: to be the bridge between the artist’s imagination and the materiality of the work. Each cast piece is a testimony to the history, passion and mastery of those who dedicate their lives to this art.
Want to know more about the foundry? You can learn more about the history of Capa Esculturas and how it has tackled projects over the years at its foundry in Madrid.